A close inspection of our chassis yielded some expensive news: major repair will be necessary.
With a 50-year-old trailer I expected to find significant rust on the steel frame. I was hoping we'd need a few patches, a few repaired welds, a good wire brushing and some rust-neutralizing paint. Unfortunately, we've got bigger problems.
While none of the frame members have separated from each other, we can see rust-through in both the C-channel cross members and (more significantly) in the box-channel rails running the length of the trailer. The back three feet of the frame are really bad. In addition to rust perforation, the last cross member was drilled several times for various plumbing and electrical needs.
You may have to click on the photos below to see the detail.

Center Section of Chassis has Rusty, but Repairable, Cross Sections
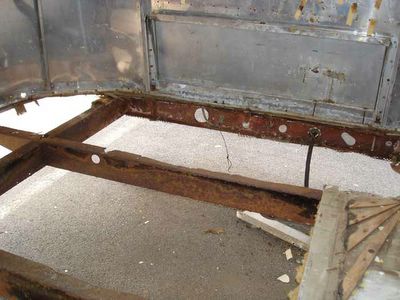
Rear Section of Chassis is So Bad it Must be Replaced
Replacing a cross member can be done by simply cutting the old one out and welding a new one in its place. The same is true for outriggers. But replacing the main rails is really impossible without effectively building a new frame.
After talking it over with Colin, I decided not to have a new frame built from scratch. Instead, we'll have Colin's welder use a combination of techniques to repair and strengthen the original chassis. It may not be as pretty as a new frame, but it will be just as strong and save a lot of money in time and materials.
Here's what Colin's crew will do:
- Cut off and entirely replace the last few feet of the chassis that are the worst. We'll have all new rails, outriggers and cross members in the back.
- Replace a couple cross members in the middle of the trailer that are beyond patching.
- Patch rust holes in all the other cross members and main frame rails that are generally good enough to save. The rust will be cut out and new steel welded in place.
- Slide new box channel inside the original box channel rails to strengthen them significantly.
This last step of reinforcing the main rails by lining them with slightly smaller box channel is a rather new tecnique Colin has developed. He's used it on other trailers with great success. It does add a little weight, but it's the most cost-effective way of getting an extremely strong frame without replacing it.