For an Airstream to be structurally sound, the floor must be solid. But I'm not talking about the part of the floor you walk on. I'm talking about the part of the floor under the walls.
When an Airstream is built, the plywood is installed first and the shell is put on top. So when the plywood around the edges softens and disintegrates, it leaves a 5/8" gap between the bottom of the wall and the top of the chassis! To make matters worse, Wally's crews usually screwed the bottom of the wall into the plywood, but not all the way through the plywood and then into the chassis. So if your floor is soft under the walls, you have NOTHING holding the shell to the chassis in the area of the weak floor!
The shell must be bolted or screwed through solid floor and into the chassis. That's why floor repair is so hard on an Airstream...and is so often done insufficiently. Floor repair shortcuts that put new pieces of floor up to the wall, but not under it, may give you a firm floor, but they will not fix the underlying problem of a shell and chassis that are not fully secured.
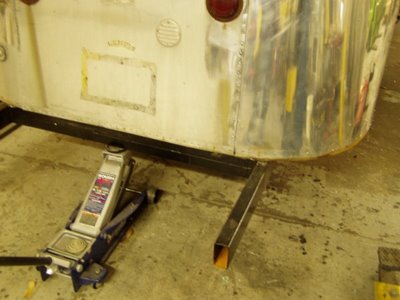
Before the plywood and chassis are fastened securely together, the chassis will have a tendency to sag at the rear end. Working on a solid level surface and using temporary jacks to hold everything straight is essential until the floor is fully fastened down. Notice, also, the extra long chassis rails. Caravanner #1 came with a 1960s-style trunk bumper for the sewer hose rather than a simple 1950s bumper. I'm going to replicate that feature.
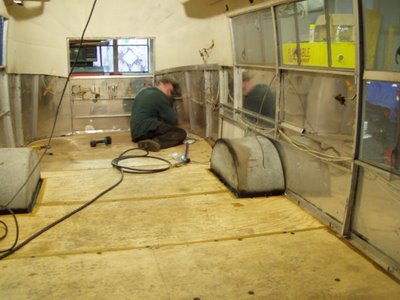
The photo above shows the new plywood floor spanning the restored chassis. For extra stability, construction adhesive is used where the floor touches the chassis. Back in the day, Wally's crews layed fiberglass insulation across the chassis before the plywood was layed. We aren't doing it that way. We'll be insulating from below before the belly pan is closed up.
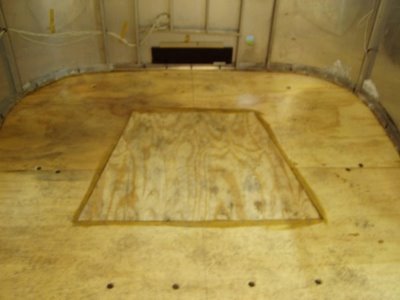
Notice the odd plywood seam pattern above. The edges of each piece of plywood need to all end up on frame members so they are supported. My chassis is modified to create a trapezoidal spare tire storage area under the floor. You can see it in post #25. This is also a good shot of how all plywood edges (and all undersides) are treated with wood preservative.
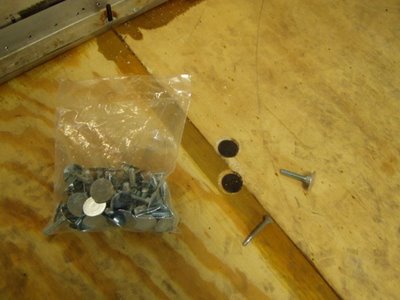
The fasteners of choice for the floor are elevator bolts and countersunk self-tapping machine screws. The elevator bolts are great because their wide flat heads are easy to countersink and could never pull through the plywood. They're secured with a hex nut underneath. The special self-tapping machine screws are almost as good. They have threads like bolts. They're used only where it would be impossible to reach the bottom end of a bolt to put on a hex nut. With the screws, the frame member is tapped so it acts like a nut and holds great. In a case like his, they aren't used much. But if you are doing a floor repair without removing the belly pan, they're your best friend.
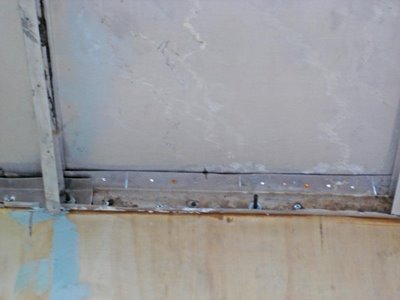
The shell has a U-channel inside the bottom edge of the wall all the way around. It's what secures the bottoms of the inner and outer skins of the trailer. Remove the lower segments of inner skin to get access to the U-channel. Screws and bolts are used to hold the U-channel to the floor and chassis. Here you can see the nuts on the ends of elevator bolts that were inserted through outriggers from below and then up through the channel. Sometimes, they go the other way. It doesn't much matter what fasteners you use here since they are hidden, but they should hold tight to the chassis as much as possible.
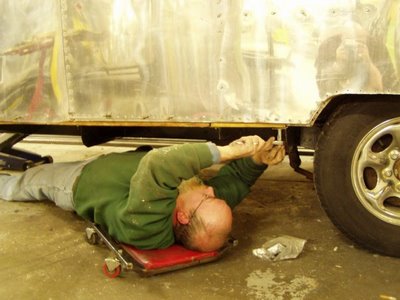
It can be tricky to get the nut on the bolt underneath. It's a two-person job. Above, Joe holds the socket wrench while Chris is working the top side.